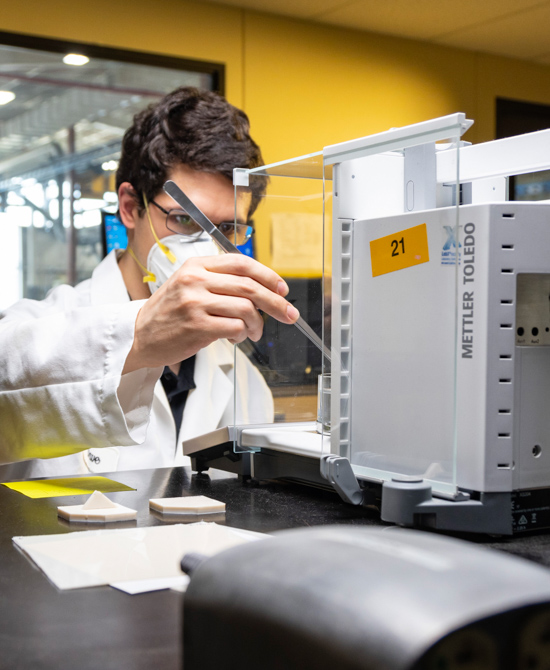
Defect-Free Materials Delivered Consistently and on Time
It’s not just a policy – it’s our practice.
Our Quality Commitment
Our commitment to our customers is defect-free materials that are delivered consistently and on-time to our customers.
Our dedication to continuous improvement and operational excellence drives every action and all of our decision-making. The goal is to earn the right for GEON to be the preferred provider of specialized materials, services and solutions to customers around the globe.
At GEON, we listen. We do it right. And we deliver.
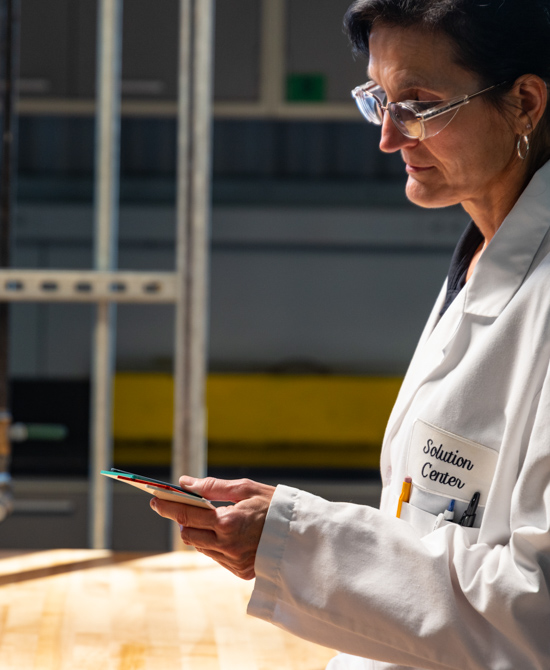
Quality Management System
Our customer-focused quality management system ensures customers experience business continuity, continuous improvement, quality supply and defect-free materials.
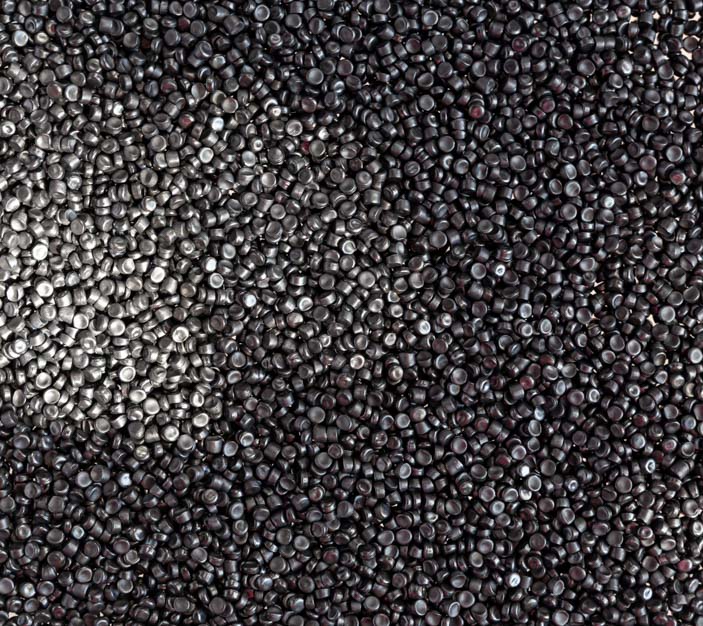
Audited annually by 3rd party
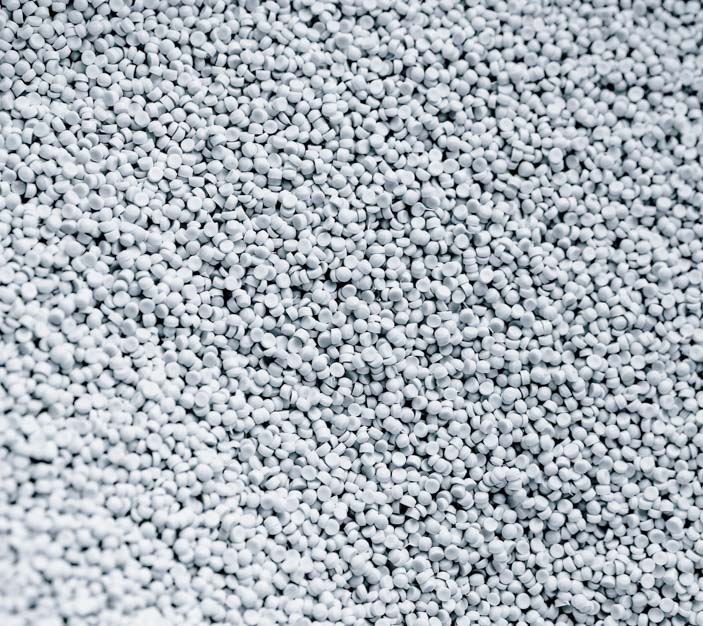
Metrics and systems drive and maintain improvements
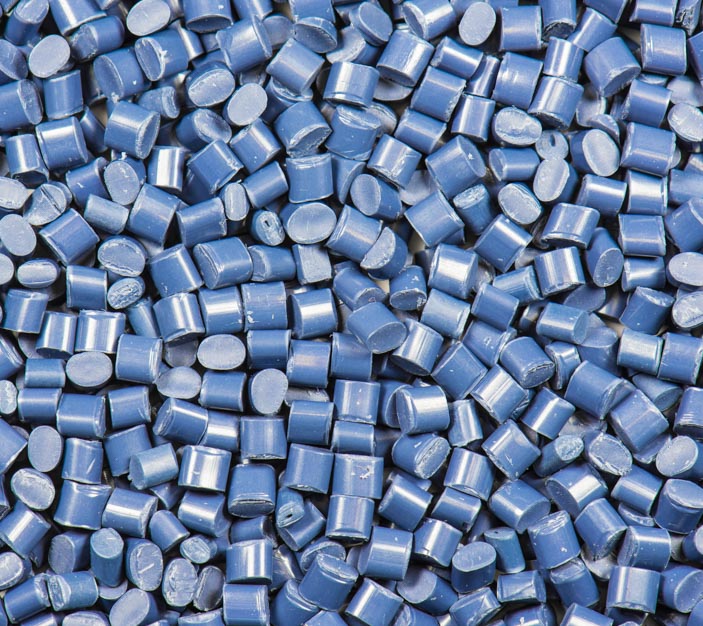
Risk management process embedded in all plants
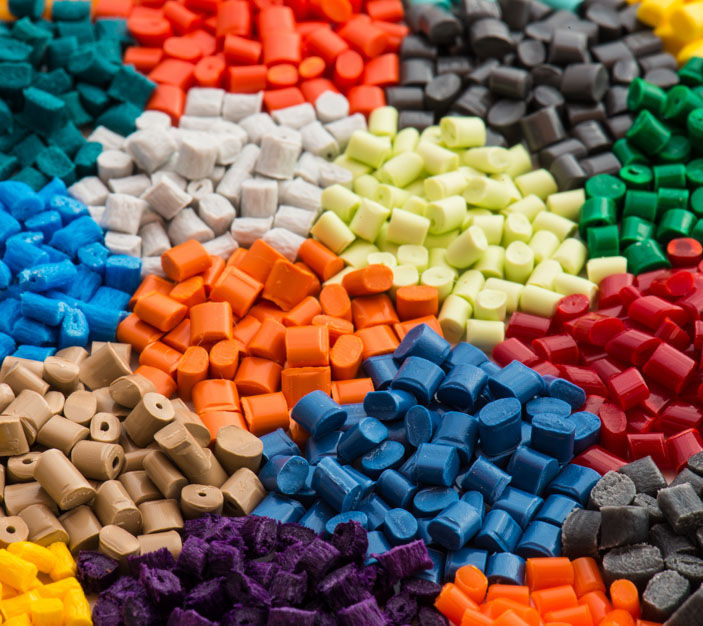
Contingency plans in place
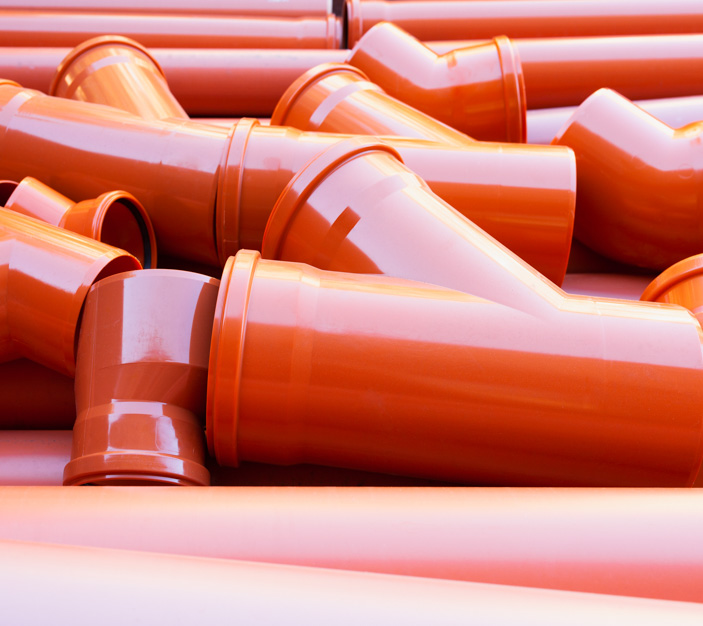
Integrated with CAPA
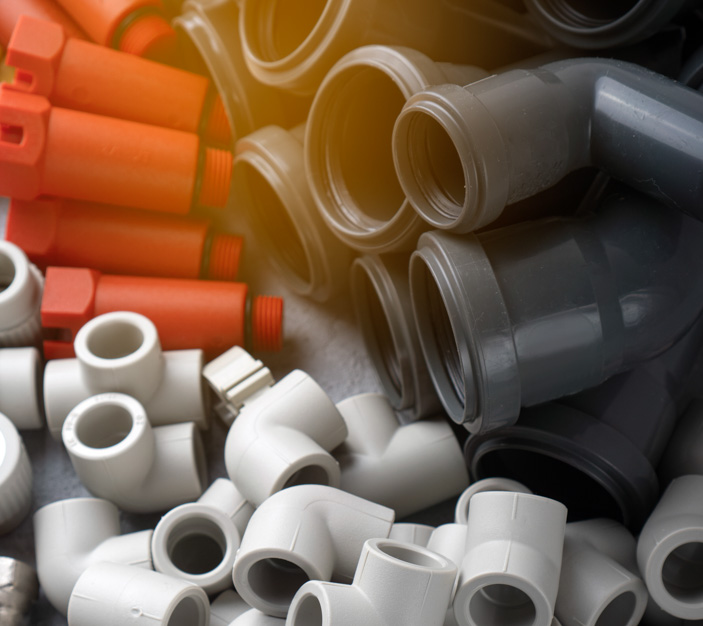
Supplier selection conforms to IATF and ISO 13485 requirement
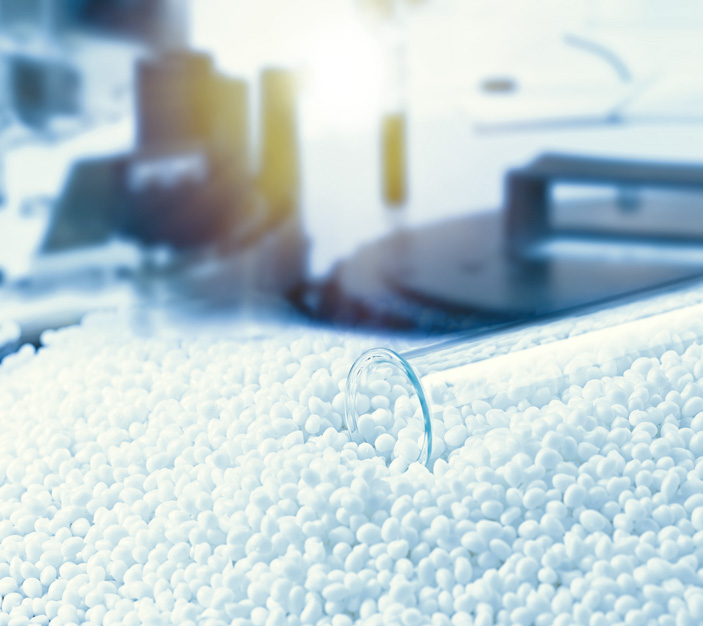
IATF 16949, ISO 9001, ISO 13485, RC14001, RCMS
Continuous Improvement Program
By applying Lean Six Sigma practices, our customers benefit from innovative processes, lower costs, cohesive operating procedures and greater satisfaction.
Certified in Lean Six Sigma (LSS), over 80 percent of our employees are LSS trained – many as project leaders and several as LSS Black Belts.
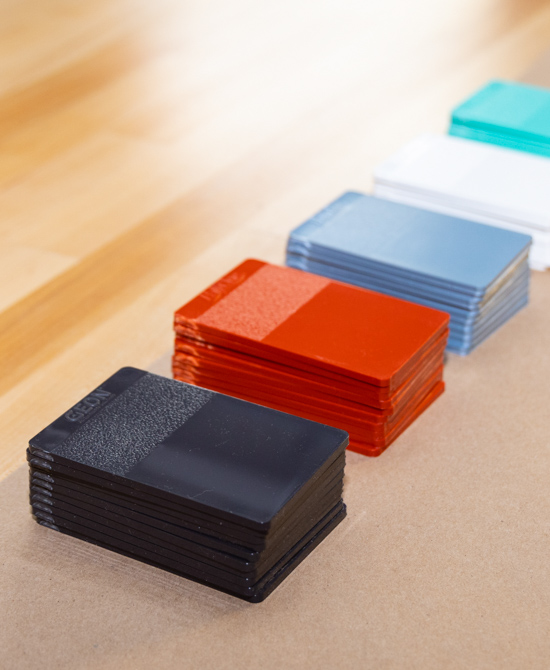
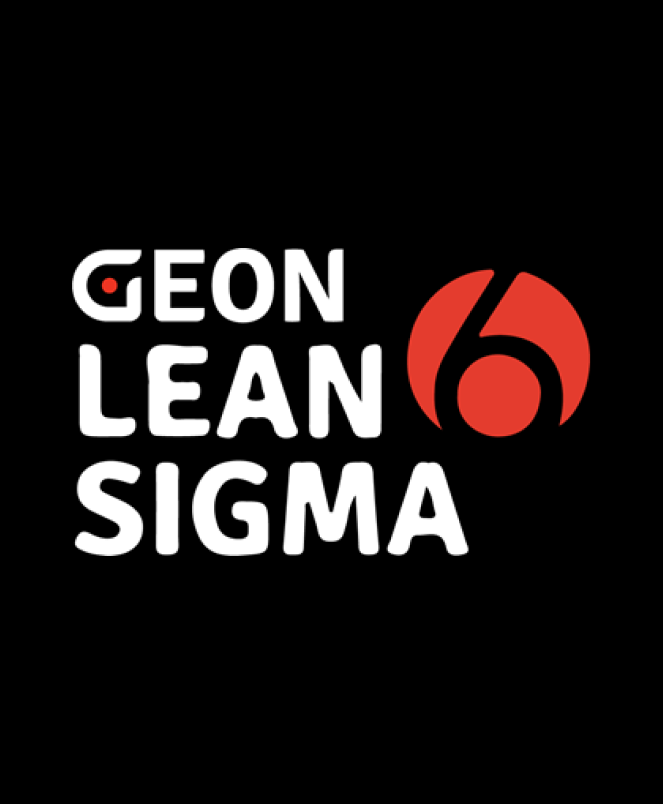
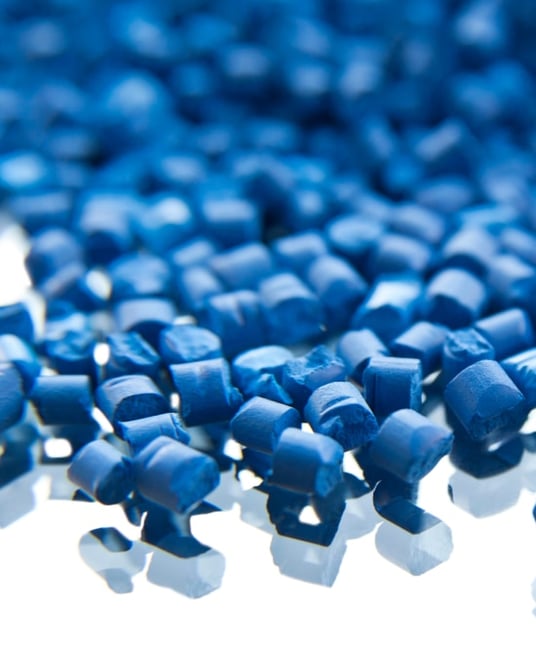
American Chemistry Council Manufacturer Member Committed to Responsible Care®
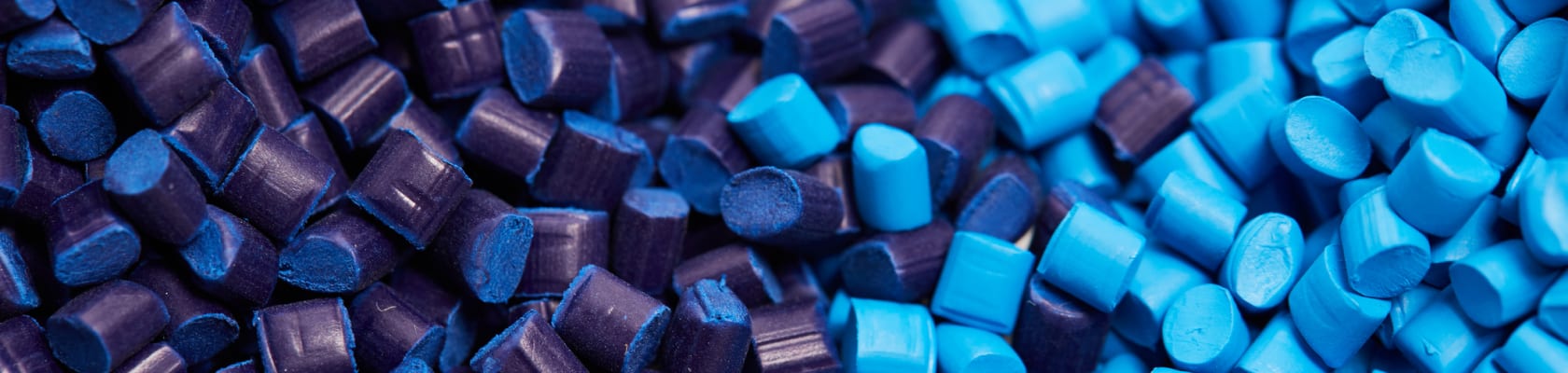