Replacing Metal with Vinyl Shines a Light on Value
Our Customer Saved $500,000 by Making the Switch From Metal to GEON® Vinyl Materials
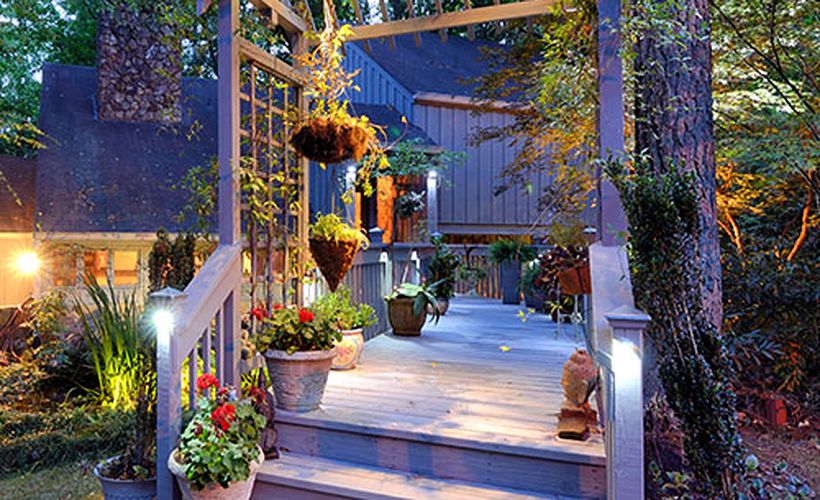
Challenge
Smart Hero, a contract manufacturer headquartered in China, produces a variety of electronic products for OEMs around the globe. While its product range is broad, this company specializes in outdoor lighting.
A team of engineers at this firm was looking for a way to reduce the manufacturing cost of its line of solar-powered lights made using painted metal. Because this supplier fabricates with both metal and plastic in its operations, the team decided to find out if converting metal parts to plastic would be an option.
At first, they experimented with pre-colored ABS, but the ABS parts failed the company’s requirements for color retention after exposure to UV light. The team then turned to GEON in Dongguan, China to see if we could offer a solution.
Solutions
Our Dongguan facility was ideally located to provide support to Smart Hero. The first step involved a meeting between our team and Smart Hero’s technical group to understand the requirements of the outdoor lighting application. The group explained that they needed a material that would exhibit minimal color change after exposure to outdoor environments.
Having experience in plastic injection molding, Smart Hero knew the material also had to have excellent flow characteristics to be able to fill the complex geometry required for the light.
Additionally, the part had to have excellent surface finish and appearance because it is a highly visible consumer part. Most importantly, the plastic light had to have lower manufacturing costs than the painted metal light.
Based on the requirements provided, we recommended GEON M5705, a high flow vinyl molding material for outdoor use. GEON provided a pre-colored version of our GEON M5705 material, customized to match the manufacturer’s gray and black painted metal lights. Samples of the GEON M5705 gray and black were placed into a trial using an existing lighting fixture to provide samples for evaluation. Our technical service representative attended the molding trials to help optimize processing conditions, resulting in the ideal parts for the evaluation. GEON M5705 material passed the company’s internal testing requirements, including color retention after exposure to UV light. The results of the evaluation gave Smart Hero the confidence to replace the painted metal with GEON M5705 material.
Impact
Moving from painted metal to pre-colored GEON M5705 material reduced Smart Hero’s manufacturing costs by over $300,000 annually, due to lower scrap rates and the elimination of painting. Further, by moving to a paintless material, this customer was able to eliminate the volatile organic compounds (VOCs) produced during paint operations, thereby improving the environmental footprint of their production facility. Due to the commercial success of the gray and black colors, Smart Hero plans to introduce seven new colors made with GEON M5705 material to expand its product line. Using GEON M5705 material for these seven colors will save an additional $200,000 per year.