An Injection Molder Switched from FR ABS to Rigid PVC and Saved $100K Annually
Surge Suppressor Housings Manufacturer Switched Polymers and Saved While Reducing Scrap Rates and Overall Production Costs
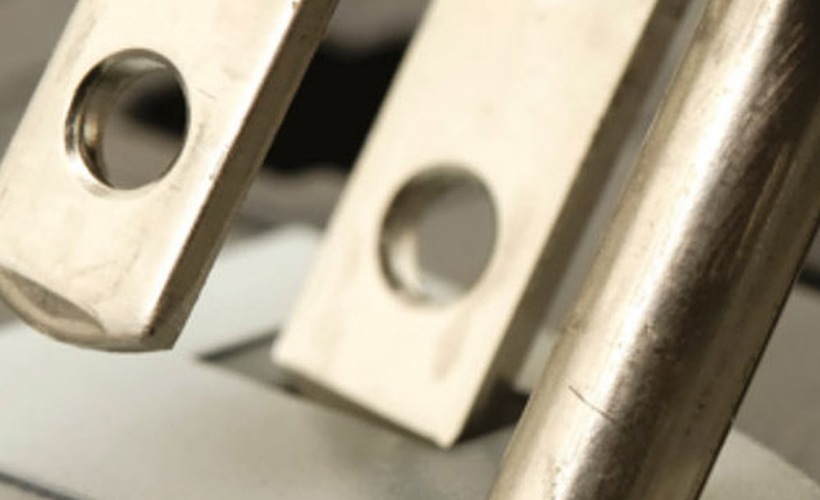
Challenge
An injection molder based in China was producing surge suppressor housings for an electrical manufacturer supplying devices to the U.S. market. The molder was using naturally flame-retardant acrylonitrile-butadiene-styrene (FR ABS) and color concentrates in white, blue, and gray colors. The FR ABS molding process resulted in scrap rates of about 15% as well as other color and appearance inconsistencies.
The molder looked to GEON® in Dongguan, China for assistance in improving the quality of production and reducing the scrap rates in its operations.
Solutions
The molder and its OEM customer met with GEON sales and technical professionals to discuss the technical, manufacturing and cost requirements for the surge suppressor housing. The material had to be UL 94 V-0 rated at 1.8 mm thickness or lower, provide very good impact resistance, and be colorable in white, blue, and gray. Additionally, the molder and manufacturer wanted the parts to have consistent color and high quality appearance.
Finally, any new solution was to lower molding scrap rates to 5% or less and reduce the overall production costs.
Based on the requirements provided, GEON recommended its GEON Rigid M3800 PVC compound, a high flow, high impact rigid vinyl molding material with a proven history of use in electrical housing applications. It has a UL 94 V-0 rating at 1.4 mm, meeting the manufacturer’s flame rating requirement.
To ensure the material would meet the customer’s financial objectives, GEON completed an economic modeling analysis which demonstrated that the customer could expect the combination of material formulation and process efficiency gains to reduce overall production costs versus the current FR ABS material. Both the molder and electrical manufacturer agreed it made sense to move forward with the GEON solution.
Switching from one polymer to another requires careful planning and a methodical approach. GEONs technical team first analyzed the existing mold and determined that GEON Rigid M3800 could be molded in the same tool with some minor modifications. Because the processor was not familiar with molding vinyl, GEON technical service worked side-by-side with them to recommend equipment and processing conditions needed to make excellent quality surge suppressor housings.
GEON was also present for initial molding trials and production start-up, which produced consistent, high quality parts and facilitated a smooth material usage transition.
Impact
By switching from FR ABS and color concentrates to GEON’s pre-colored Rigid PVC, the electrical manufacturer was able to meet its end-use requirements, improve manufacturing efficiency, and reduce operating costs by about $100,000 a year.
With its flame, chemical, and UV resistance, GEON vinyl is an exceptional choice for applications requiring performance and quality. GEON not only added value with a material, but also provided exceptional service to facilitate an efficient conversion from FR ABS to GEON Rigid M3800 vinyl.